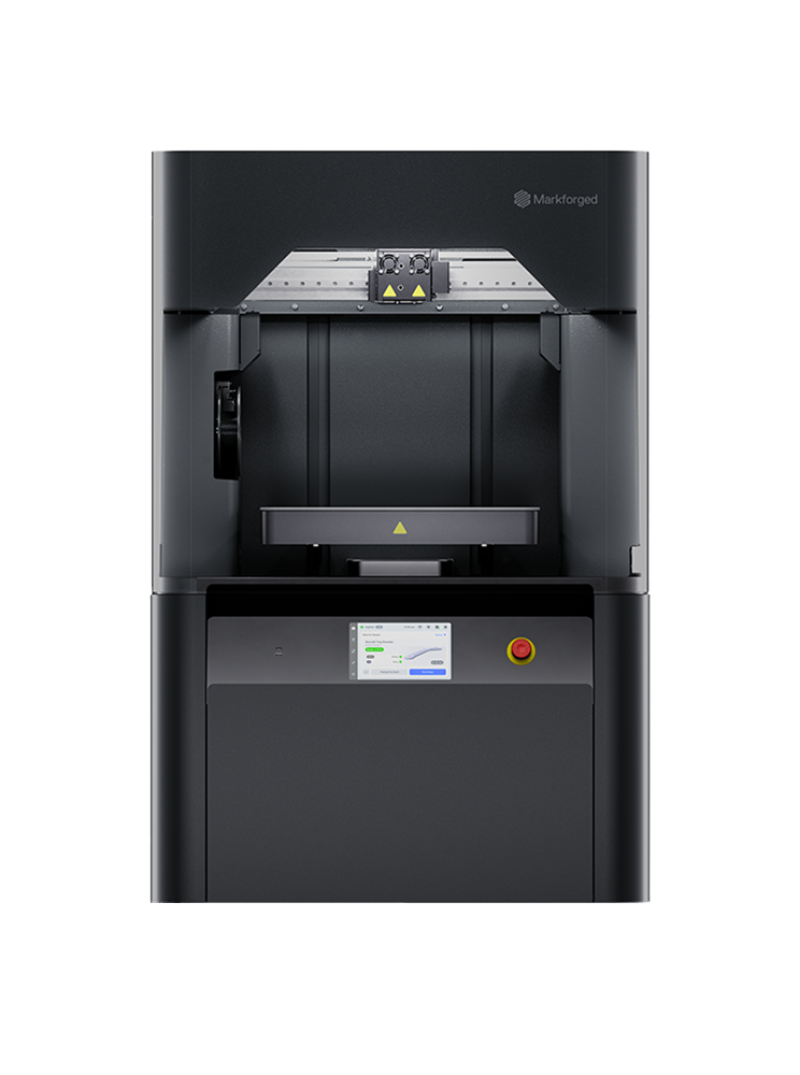
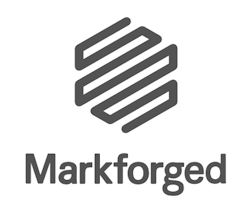
FX10 – Next-Gen 3D Printer for Innovation & Production
Print continuous carbon fiber reinforced parts for a wide range of factory floor applications — deliver strong, accurate parts for every print.
► Build Volume (375 mm x 300 mm x 300 mm)
► Layer Resolution of 125 μm – 250 μm
► Printing Process Fused Filament Fabrication, Continuous Fiber Reinforcement
► Access to High-Strength Materials – Onyx® and Continuous Carbon Fiber
Meet FX10 – The Most Versatile Tool for Your Factory Floor
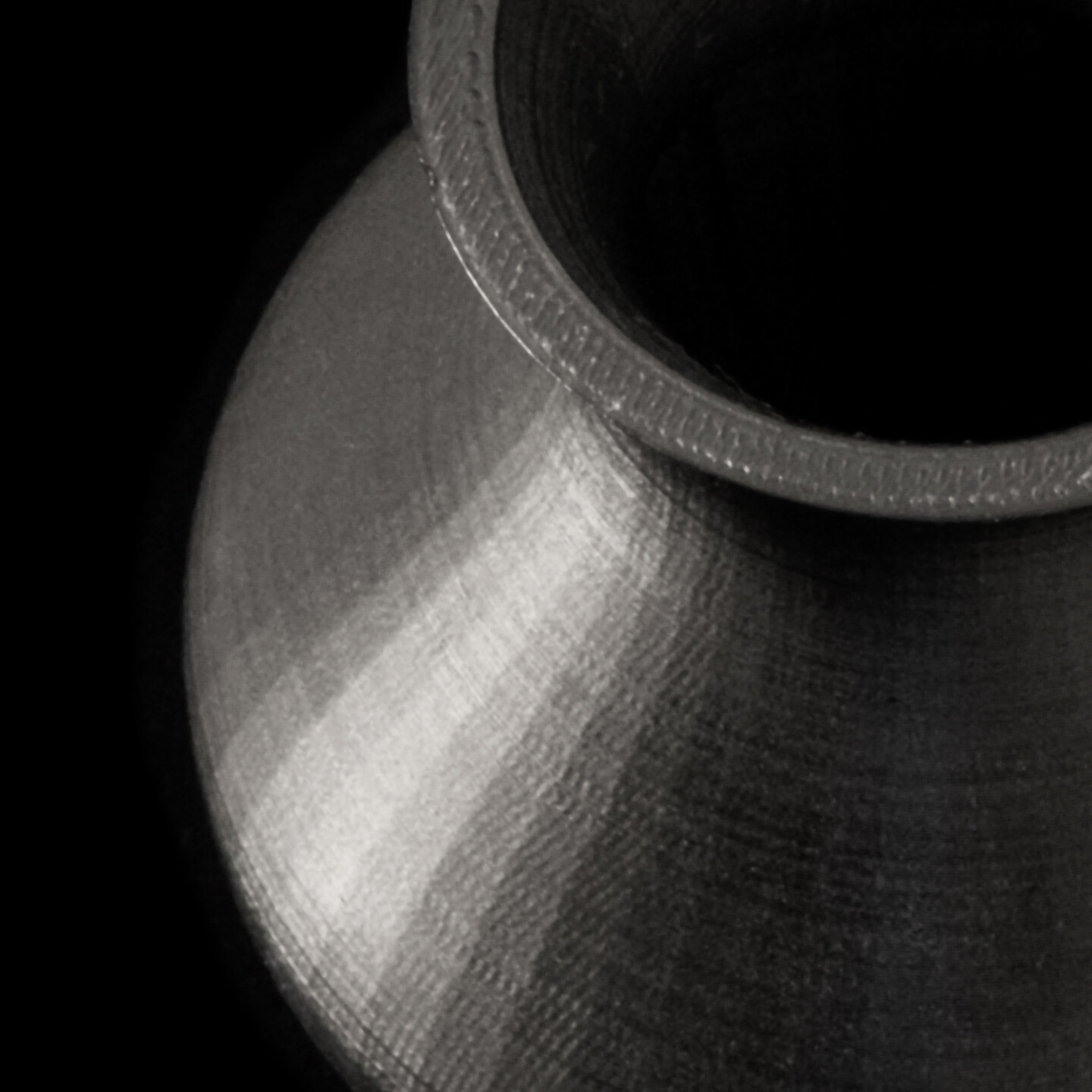
SPECIALIZED PRINTING TECHNOLOGY
UNLOCK STRONG PARTS ON DEMAND
Increase manufacturing speed and time to market, slash fabrication and inventory costs, with strong lightweight parts with remarkable surface finish.
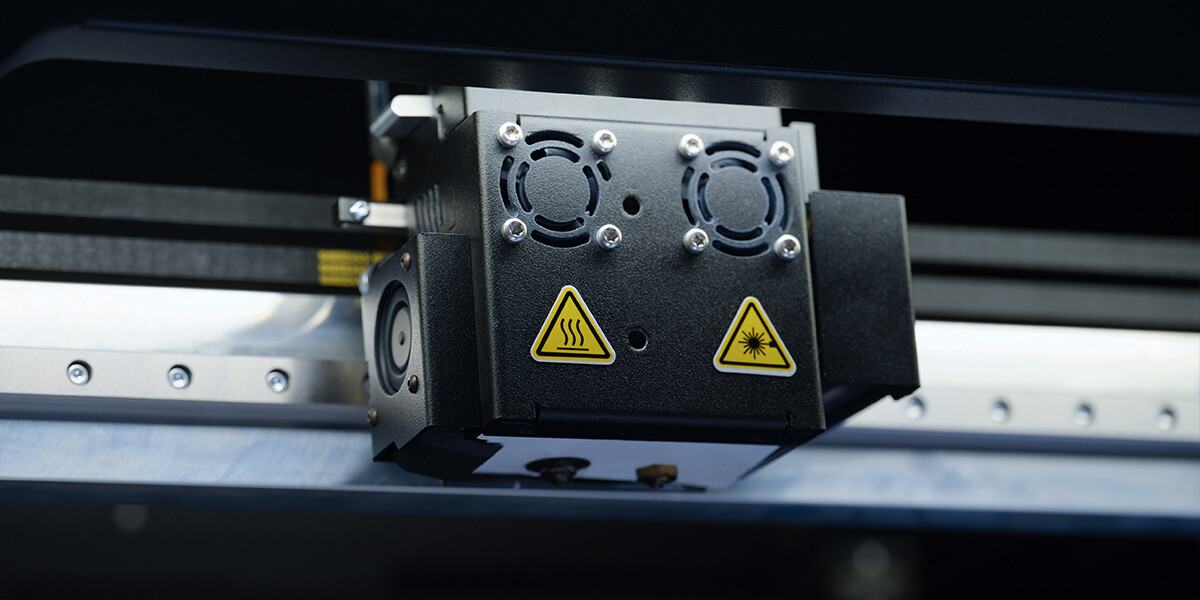
HIGH-ACCURACY RESULTS
PRINT THE RIGHT PART EVERY TIME
We designed every aspect of FX10 — from its motion system to the software that powers it — around delivering accurate, strong parts reliably.
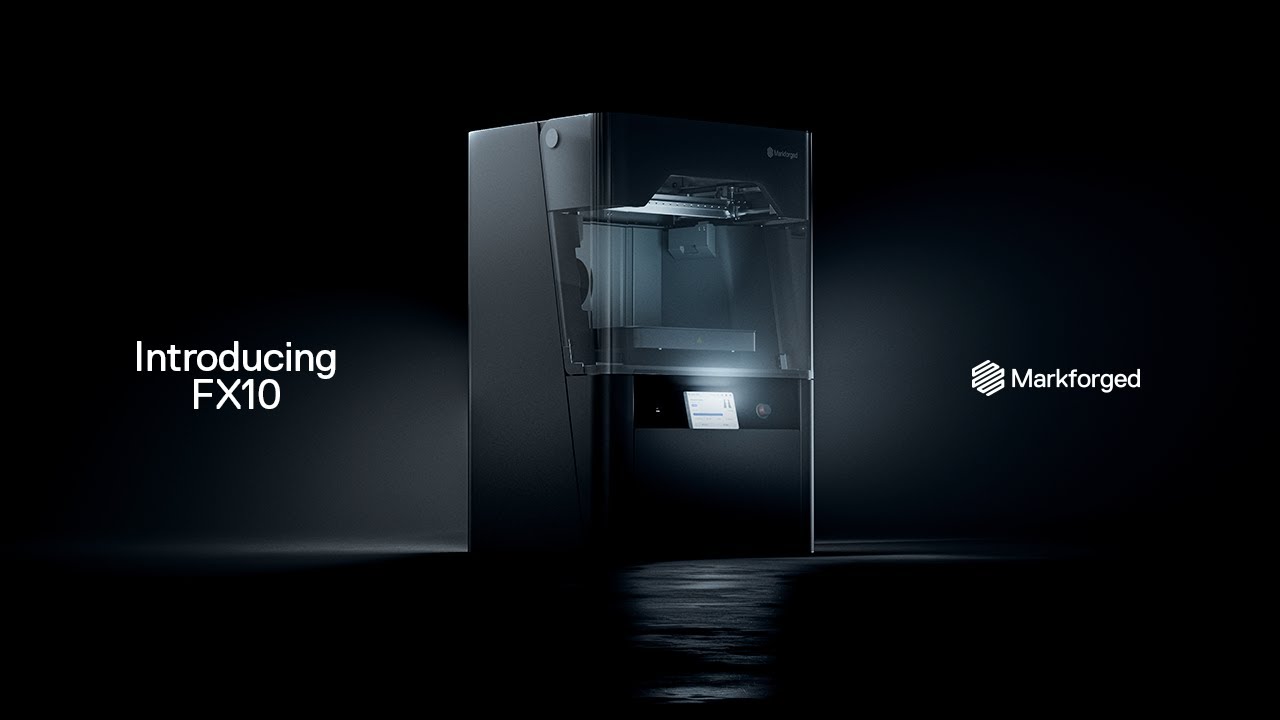
FOR BEGINNERS & ADVANCED
QUICKLY DRIVE ROI AND FUEL YOUR BUSINESS
You can start generating ROI on day one and effortlessly scale to more teams, machines, and facilities.
The FX10, Markforged’s cutting-edge industrial composite 3D printer, represents the culmination of extensive engineering innovation and technological advancement. Evolving from the success of the Markforged X7, its primary objective is to consistently produce robust, precise parts with each print.
Massive Builds, Faster
FX10 features two print head mounted optical sensors. The laser micrometer powers Inspection — in-print dimensional validation — and machine calibration while the new Vision Module will capture detailed images of calibration parts to determine and optimize printer performance.
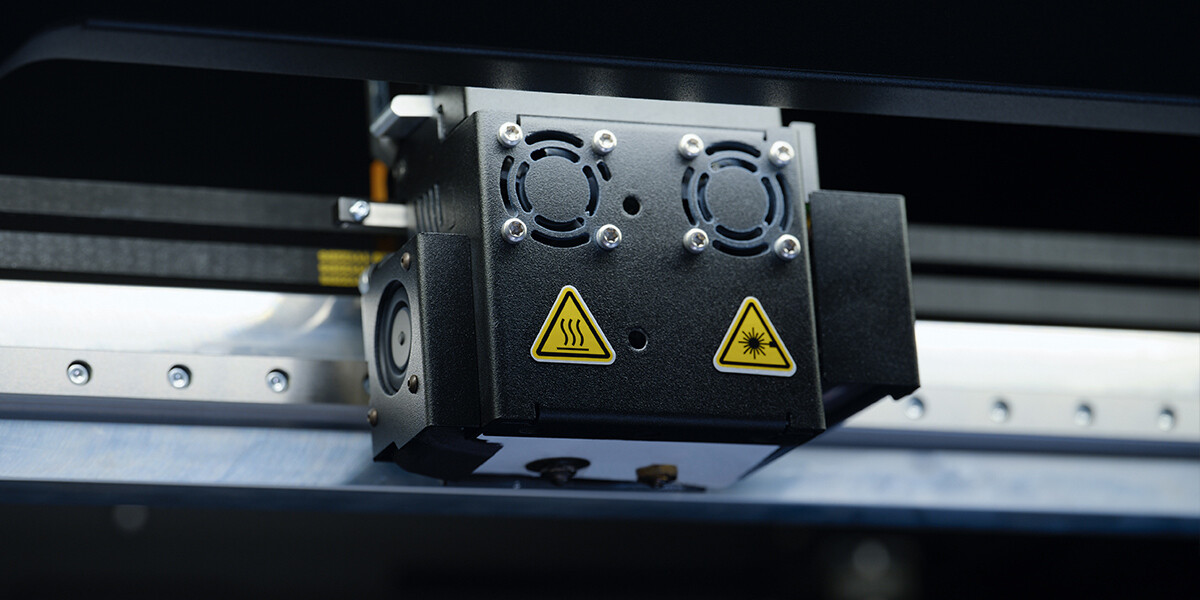
Advanced Material Chamber
An inboard material chamber stores four spools in individually sealed compartments and supports auto material changeover and fast spool loading, reducing user intervention.
Compatible Materials
- ONYX
- Carbon Fiber
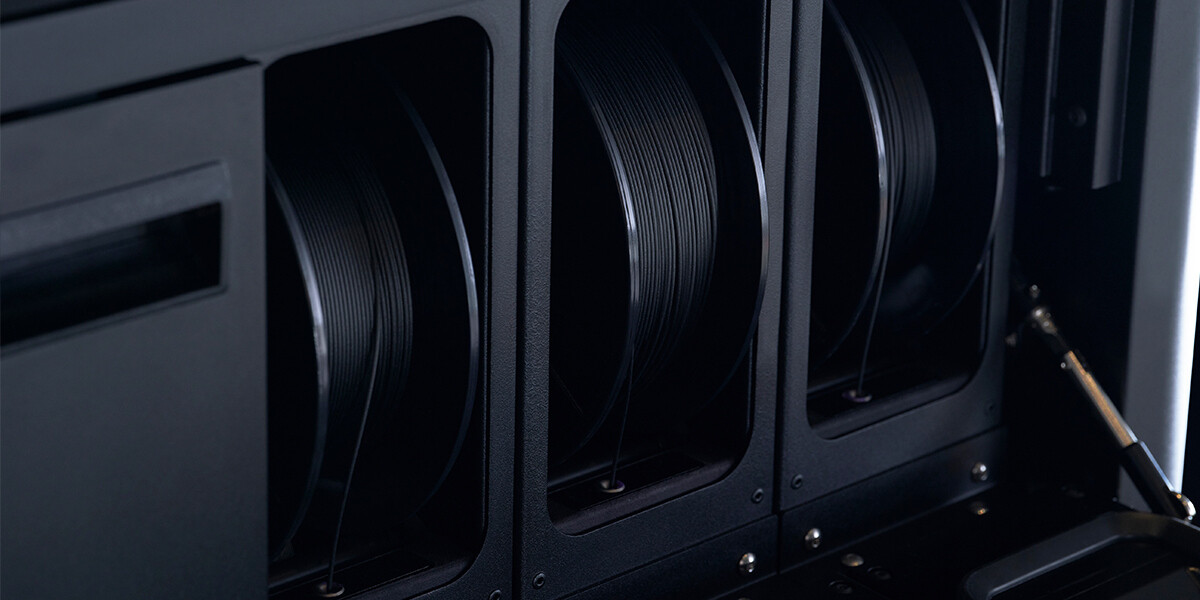
Heated Build Chamber and Vacuum Bed
The FX10 has a large chamber that heats to 60 °C, useful for printing high-quality parts at high speed. The aluminum vacuum bed is also heated and utilizes precision-machine grooves that are scanned by the laser micrometer for calibration..
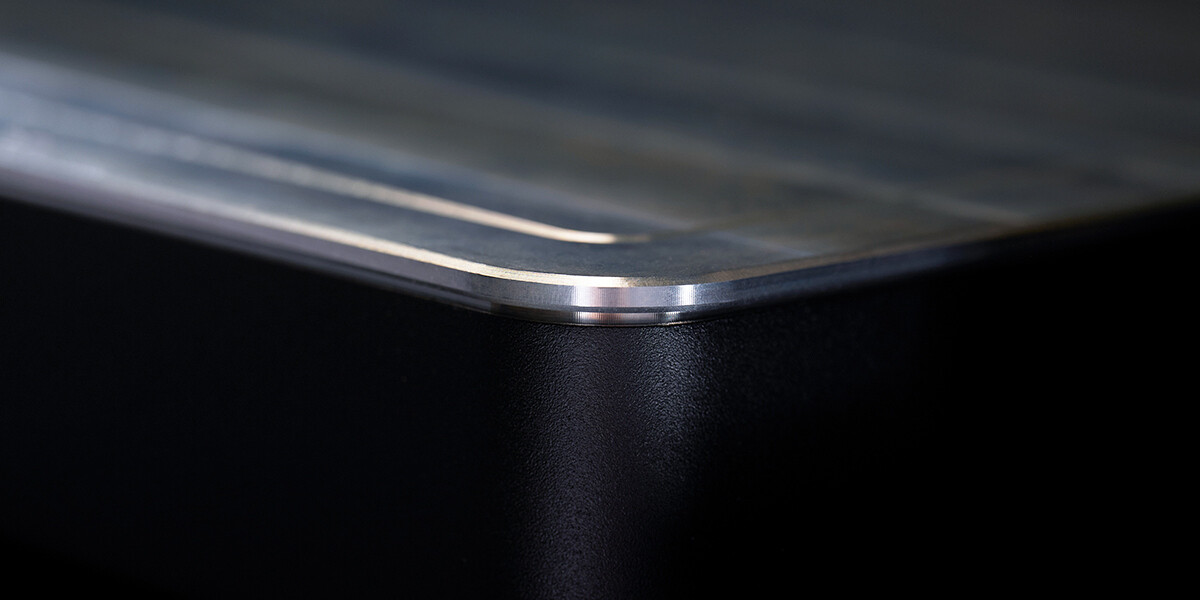
SOLVE BIGGER, AND MORE COMPLEX CHALLENGES
Functional parts, made EASY.
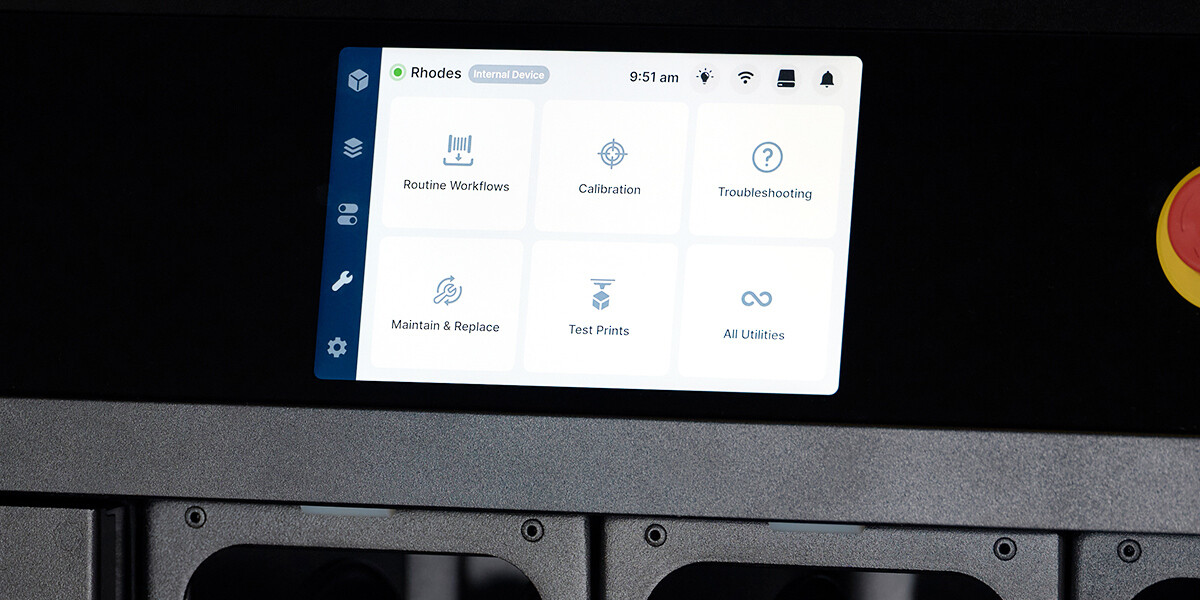
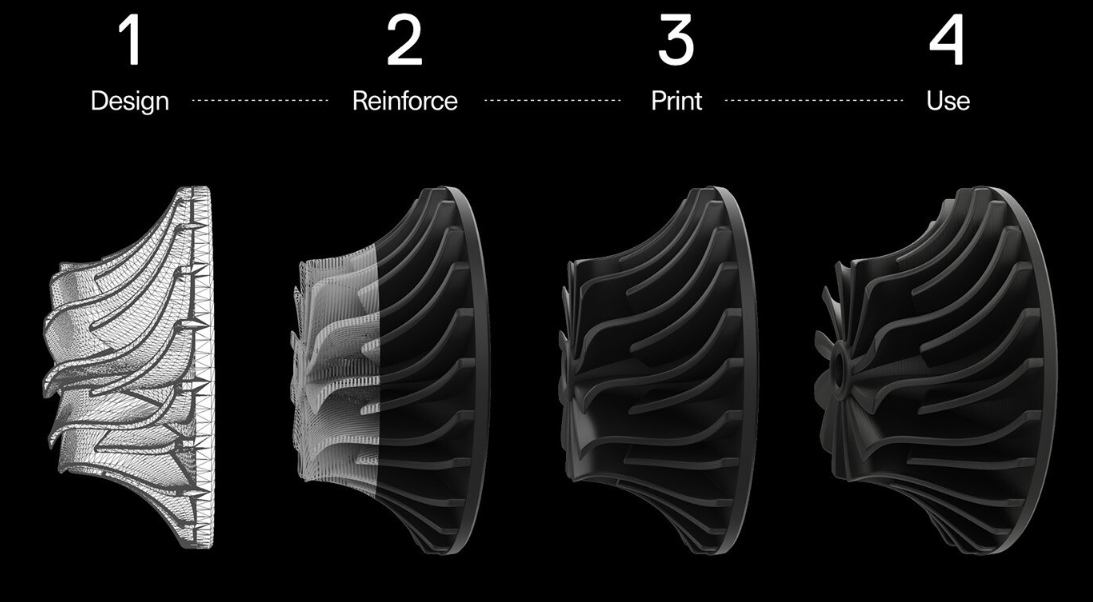